Communications and Marketing
Jet Fuel from sewage sludge and biowaste: H-BRS draws up life cycle assessment
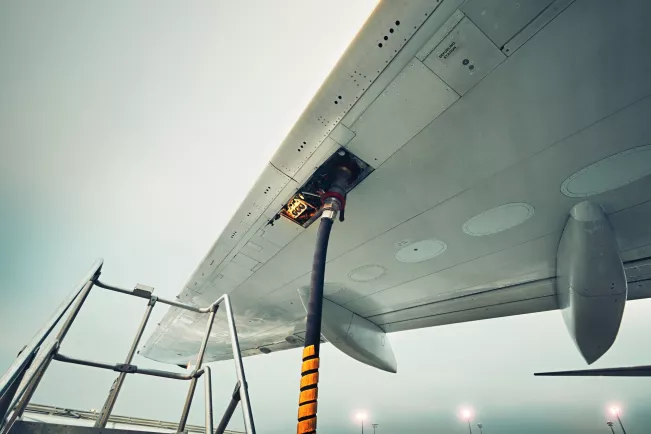
CO2-neutral lying with the help of sewage sludge and organic waste - this is a very simplified description of the idea behind the reTURN research project (recycling organic residues and CO2 into fuels). By producing climate-neutral synthetic fuel to replace fossil fuel, the aim is to drive forward the energy transition and contribute to global climate protection. "The aviation industry cannot be completely electrified," says Professor Stefanie Meilinger, who is leading the project at H-BRS. "Moreover, flights can perhaps be reduced, but not completely prevented. That's where we need other solutions." That also applies to some areas of trucking or shipping, she adds.
One technology for producing synthetic fuels has been developed by the company Caphenia. The idea is to combine three known chemical processes in a single reactor, one after the other and in three steps, to produce a synthesis gas. The starting materials are biogas (consisting of methane and carbon dioxide) produced from organic waste and sewage sludge, water and electricity from renewable sources.
First, the methane is broken down into its carbon and hydrogen components using renewable electricity. In a second process step, the carbon reacts with the carbon dioxide to form carbon monoxide. In step three, carbon monoxide is also formed from further carbon and water vapor, but hydrogen is also produced - so the overall result is a mixture of carbon monoxide and hydrogen. This synthesis gas can then be converted into any fuels such as kerosene, diesel or gasoline using known conversion technologies. In 2021, the company was nominated for the German Innovation Award for the development of this process.
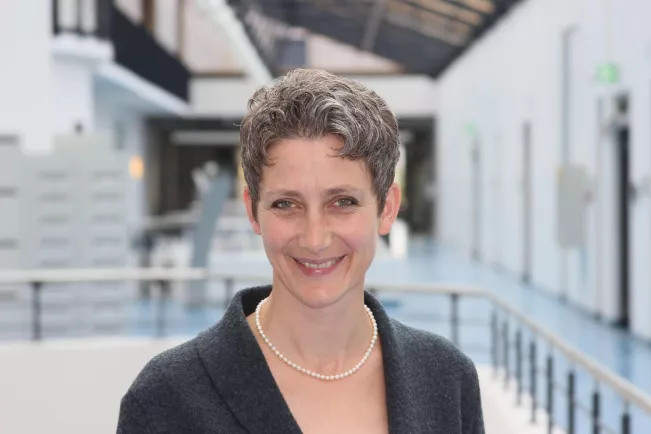
Now the process is entering a four-year practical test in the reTURN project: A prototype of the reactor will be built in Frankfurt-Höchst starting in 2023 and the process will be tested to prove its technical feasibility and suitability for the mass market. As the second project participant, the Institute of Combustion Technology of the German Aerospace Center (DLR) is designing measurement methods on the reactor and simulations. Bonn-Rhein-Sieg University of Applied Sciences is developing a model to determine the CO2 footprint throughout the process and in the test plant.
"We are accompanying the construction of the test reactor with a life cycle assessment and preparing a complete life cycle analysis," says H-BRS Professor Stefanie Meilinger. The materials needed to build the reactor are examined for their CO2 footprint, as are the provision of the biogas and the synthesis gas production itself. However, the ecological sustainability assessment goes even further. H-BRS is developing a model that not only represents the actual state of the test reactor, but also takes into account the interdependencies of all parameters and can thus be variably adapted for different site conditions.
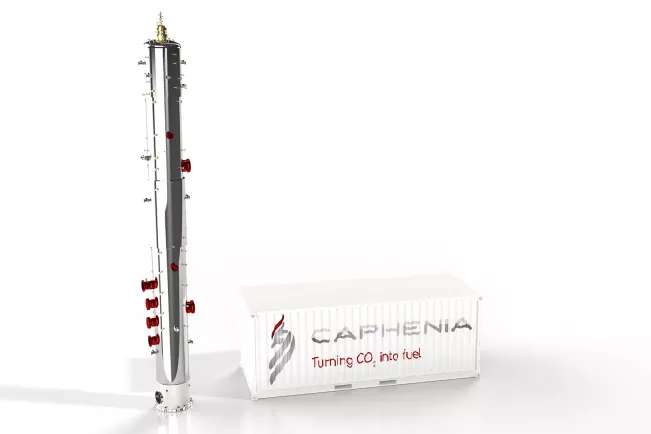
"Our hope is that this new process will require much less energy than other processes," says the H-BRS professor, whose research focuses on sustainable technologies. "And from the biogas, not only is the methane used, but also the carbon dioxide, which further improves the balance."
Fundamentally, it is important to Meilinger that technological developments and ecological assessments are brought together. "To achieve the energy transition, we need to consistently study each technology, discuss the alternatives and calculate their life cycle assessments," she says. "We always need to look at how the processes compare." That's also something she hopes to teach her sustainable engineering students in "life cycle assessment" (LCA), which is one of the university's specialties.
Background: 3-in-1 zone reactor
The reactor is divided into three superimposed areas. The process begins in the upper area, known as the plasma zone, with the thermal process of plasma pyrolysis. Methane (CH4) is introduced here and heated to around 2,000 degrees Celsius. Heating takes place with an electric arc, i.e. by applying current. During plasma pyrolysis, each methane molecule decomposes into one carbon atom (C) and two molecules of hydrogen (H2).
These reaction products are fed into the middle chamber. Here, in the Boudouard zone, carbon dioxide (CO2) is introduced to exploit a reaction discovered by Octave Leopold Boudouard (1872-1923). The carbon dioxide reacts with carbon to form carbon monoxide (CO).
In the hetWGS zone (heterogeneous water-gas shift reaction), water is introduced, which also reacts with the hot carbon to form carbon monoxide (CO) and hydrogen (H2) - the two components of the synthesis gas. The CO-H2 ratio is adjustable.
Press images
Kontakt

Location
Sankt Augustin
Room
E 240
Address
Grantham-Allee 20
53757, Sankt Augustin
Telephone
+49 2241 865 9560